Top 6 Ways to Implement a Safety Culture
Workplace injuries cost American businesses billions of dollars every year. According to OSHA, employers pay $1 billion per week in workers’ compensation costs. Some costs come from the days that injured employees miss work. Injuries and accidents force injured employees to miss at least six days of work per year. This costs employers in the United States about 62 billion dollars a year. Having a safety culture in your organization will go a long way in reducing these costs. This can be prevented by taking courses like OSHA 10-Hour and OSHA 30-Hour.
Most workplaces lack a safety culture where both managers and employees prioritize safety. It is about changing the culture, not just changing the tool. Having workers follow the proper safety procedures and use safety tools and gear will not happen overnight. There is a learning curve that comes with safety tools and procedures, but there needs to be a willingness to change.
Most Construction Workers have been using the same tools and performing the same tasks for ages. Changing their attitudes about new safety tools and procedures can be challenging. Employees, particularly the older ones, are very often resistant to change. They get comfortable using their old tools. They are not too keen to use newer and safer tools. Safety managers often face this problem when getting workers to use new safety tools.
Companies should view improvements in their safety culture as an investment, rather than a cost. Having a robust safety culture is about keeping employees healthy. All employees deserve to spend quality time with their families. And this will be possible only when employers take care of their employees’ safety and health.
Here are 6 ways to implement a safety culture in the workplace:
Safety Culture Starts at the Very Top
An important part of any workplace culture is when employees feel like their company cares about them. Companies should view safety as a health issue, rather than a cost issue. Companies should personalize all safety communication and offer courses like OSHA 30 for employees to build a safety culture. Employees will feel good about themselves if they see their employers taking a keen interest in their well-being. If top-level managers genuinely care about the safety of their workers and the workers are aware of that, they will develop a positive attitude towards safety. By showing genuine care for employees, employers will be able to convince even the most resistant employees to embrace a safety culture.
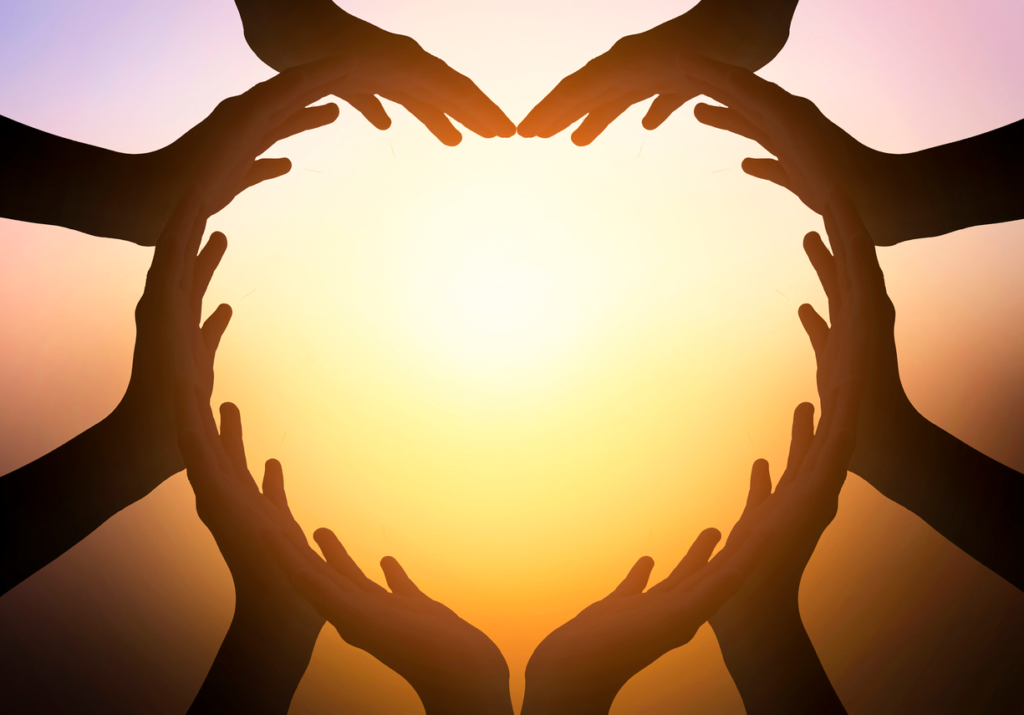
Dispel the Negativity towards a Safety Culture
Identify workers who are not interested in changing the tools and procedures they are comfortable with. Companies first need to address this resistance to change. Try showing workers examples of safety precautions they may already be familiar with but may not even think of as safety precautions. It may be safety gear they already use, such as gloves, or a safety precaution like cleaning up spilled liquids to prevent slips and falls. It is likely these workers already follow plenty of such safety precautions. Emphasize the importance of those precautions. Show them how the new safety precautions are just as important for their safety as the existing ones.
Implement a Preventive Safety Measures
Most companies have a very reactive approach towards their safety culture. They begin making changes to safety protocols only after an injury or incident has occurred. Only companies taking a proactive approach can claim to be safety leaders. Don’t be forced to learn safety because of an accident. Avoid injuries before they even happen. For example, if you are a safety manager at a paper mill, the workers in your organization most likely wear steel-toed shoes, eye-protective gear, and ear protection because of previous accidents that were common decades ago. Go a step further by considering all the other accidents that could occur. Conduct research to find out about the accidents that have taken place in the industry and what safety precautions companies took as a response. It is important to take safety precautions before incidents occur.
Identify Early Safety Culure Adopters
Identify leaders in your company who wield influence among their teammates. Use them as anchor points for promoting a safety culture. It could be a manager or a popular employee who is likely to easily adopt safety procedures. Find someone you can trust that will is open-minded. Once they are convinced that the new tools or methods will prevent company injuries, such an individual will help implement a safety culture throughout the organization. Their attitude towards safety will eventually spread to people who were resistant because they will have the credibility to get their ideas or habits adopted.
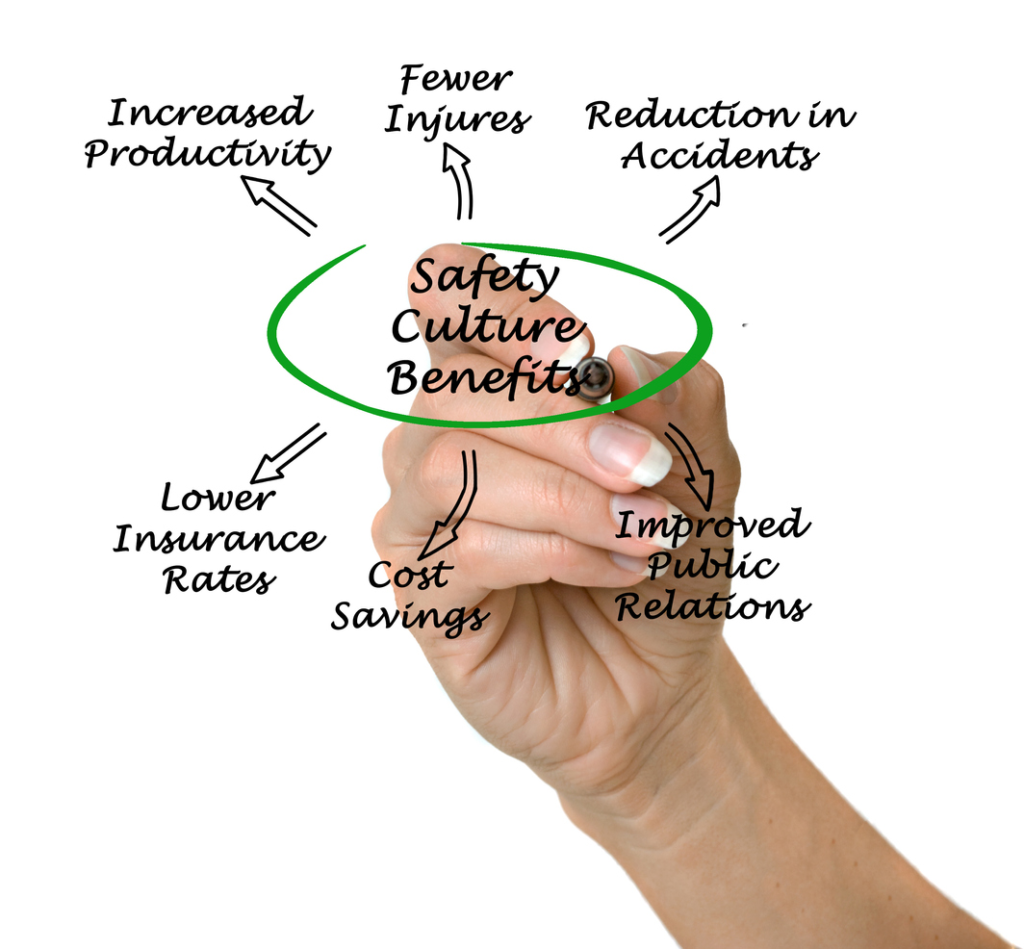
Safety should be Celebrated and Rewarded
Companies should show appreciation for employees embracing a safety culture. They should also celebrate and have material rewards for safety achievements and milestones. Companies can communicate their recognition of these initiatives by displaying posters showing how many days it has been since an injury occurred. Sometimes you just need verbal appreciation to keep your workforce motivated. Promoting a positive vibe around safety efforts will influence your workforce to think positively about safety.
Include Safety Education in Safety Training Programs
Most safety training programs focus on training workers on how to use safety tools and teaching them the safety precautions for every application they are tasked with. However, it is also necessary to educate employees on the importance of safety through OSHA courses as well as proving them OSHA-approved certification such as OSHA 30 certification. Walk them through the potential injuries that can occur and the danger of not following safety procedures. If they have a better understanding of why the safety procedures are so important, they are more likely to follow them.